公司是中国活性炭过滤器和化学过滤器系列产品的专业活性炭过滤器厂家,致力于提供活性炭过滤器、活性碳过滤器、活性炭空气过滤器、化学过滤器以及初中高效空气过滤器、空气净化设备等无尘室设备,公司拥有专业的空气过滤器研发及制造中心,专注于各种活性炭过滤器及空气过滤器和活性炭净化设备等产品的研发及生产,全系列空气过滤器年度生产能力在30万只以上,拥有国际先进的数条自动化生产线及检测设备,是国内专业的活性炭过滤器生产厂家之一。详情请点击“公司简介”
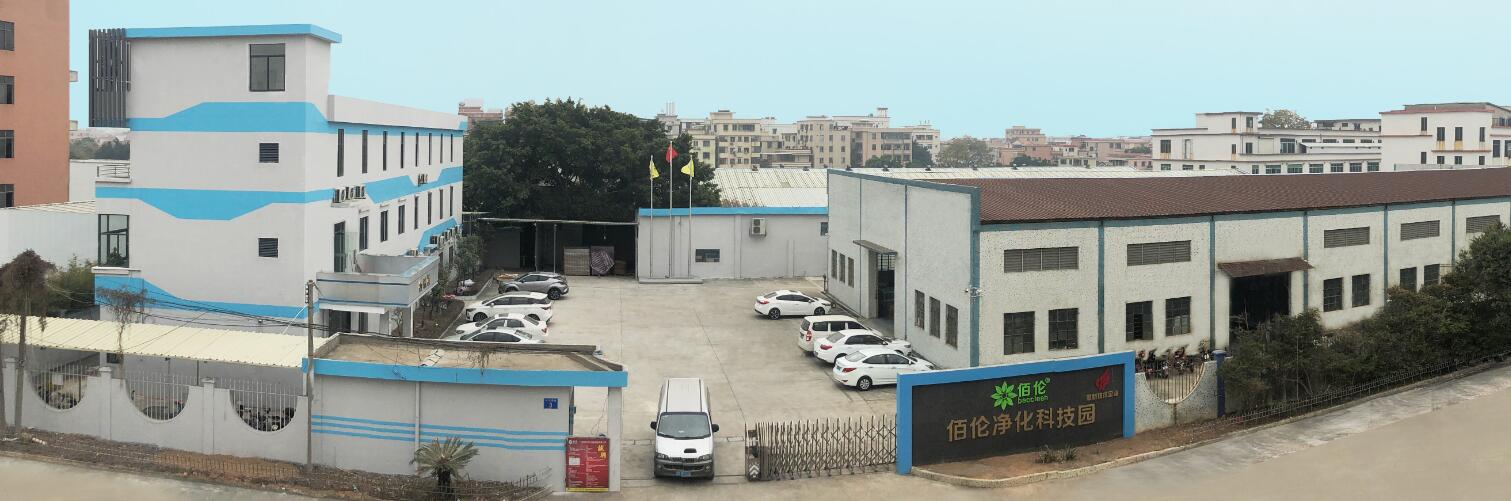
折叠式活性碳过滤器
折叠式活性碳过滤器又称为折叠式活性碳过滤网,折叠式活性碳过滤器主要以活性炭棉为滤料
箱式活性炭过滤器
箱式活性炭过滤器(箱式活性炭空气过滤器)采用高吸附性的超越活性的炭纤维或炭毡为吸附滤材
组合式活性炭过滤器
组合式活性炭过滤器也叫V型活性碳过滤器,主要采用的颗粒状活性炭,如椰壳活性炭、柱状活性炭等
箱式化学过滤器
箱式化学过滤器是根据现代医院感染控制发展的需求,在总结以往过滤器滤菌不灭菌
活性炭净化装置
活性炭净化装置又叫活性炭吸附塔净化装置,是一种高效率经济实用型有机废气的净化与治理装置。
活性炭过滤棉
活性炭过滤棉是在聚氨酯泡棉上载附粉状活性炭制成,其含碳量在35%-50%左右,具有良好的吸附性能
高效过滤网
高效过滤网主要分为有隔板高效过滤网、无隔板高效过滤网、耐高温高效过滤网
风淋间
风淋间是人员进出洁净室的必经通道,通用性强,是生物洁净室及洁净厂房的理想配套设备
版权所有 ©2012 Http://www.ihepafilter.com/ All Rights Reserved
活性炭过滤器厂家生产品牌活性炭过滤网包括:活性炭过滤器,活性碳过滤器,高效活性炭过滤器,活性炭空气过滤器,化学过滤器等,是国内专业活性炭过滤器生产厂家之一,欢迎来电咨询! 网站地图 标签